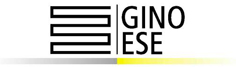 Bremswiderstände
Funktion
Die Drehzahl eines Drehstrom-Kurzschlussläufermotors ist sinnvoll nur über die Änderung der Frequenz der speisenden Spannung steuerbar. Hierzu werden Frequenzumrichter (FU) eingesetzt, deren Ausgangsfrequenz unabhängig von der Netzfrequenz steuerbar ist. Der Drehstrom des Netzes wird zunächst in einem Zwischenkreis in Gleichstrom und dann in einen Drehstrom mit änderbarer Frequenz umgewandelt.
Für Antriebe die im I. und III. Quadranten des n/M Diagramms arbeiten, das sind Antriebe deren Trägheitsmoment erheblich kleiner ist als das Lastmoment, können Frequenzumrichter unverändert eingesetzt werden. Vierquadrantenantriebe erfordern jedoch eine Zusatzeinrichtung zur Aufnahme der kinetischen Energie.
Solange der Motor belastet ist, eilt sein Anker der Frequenz der speisenden Spannung hinterher (Schlupf). Verringert der FU seine Frequenz oder wird der Motor durch äußere Betriebsbedingungen getrieben (Senken, Bergabfahrt), ist die Läuferfrequenz höher (übersynchron), als die des speisenden FU. Der Motor wird zum Generator.
Die generatorische Energie führt zur Spannungserhöhung im Zwischenkreis des FU und muss abgeführt werden. Die Rückspeisung ins Netz ist aber nicht in allen Fällen wirtschaftlich sinnvoll.
Erstens muss das speisende Netz in der Lage sein die Energie aufzunehmen und zweitens muss die Energie so aufbereitet werden, dass sie ins Netz zurückgespeist werden kann. Dazu ist ein zusätzlicher u.U. hoher technischer Aufwand erforderlich, der die Investitionskosten und die Komplexität der Anlage erhöht. Insbesondere wenn hohe Bremsenergien kurzzeitig auftreten und die gesamte Bremsenergie relativ zum Energiebedarf des Antriebs gering ist, ist es ökonomischer, sie in einem Bremswiderstand in Wärme umzuwandeln.
Ein elektronischer Schalter (Chopper = Zerhacker) schaltet den Widerstand ein, bevor die Zwischenkreisspannung eine für die Komponenten gefährliche Höhe erreicht. Der Widerstand belastet die Zwischenkreisspannung. Sobald sie einen Pegel erreicht, der kleiner ist, als die Einschaltspannung, aber größer als die Netzspannung, schaltet der Chopper den Widerstand wieder ab. Der Vorgang wiederholt sich, sobald die Spannung wieder ansteigt, wobei - abhängig von den Zeitkonstanten des Kreises - Frequenzen von einigen hundert bis zu mehreren tausend Hertz erreicht werden. Der Widerstand wird mit einem gepulsten Gleichstrom betrieben, entnimmt dem Antrieb die Energie und bremst ihn ab. Die Energie wird in Wärme umgewandelt und an die Umgebung abgegeben.
Auswahl
Bremswiderstände kommen zum Einsatz bei Hub- und Fahrwerken, Aufzugantrieben, Fördergeräten, Antriebe an Handhabungsgeräten sowie allen Antrieben, von denen durch Steuerung oder Regelung schnelle Drehzahländerungen gefordert werden und die überschüssige Energie nicht von den Lasten oder Verlusten der Arbeitsmaschine aufgezehrt werden.
Widerstände für kleinere Leistungen können dabei zusammen mit den übrigen Geräten in der Schaltanlage eingebaut werden. Wegen der Wärmeentwicklung haben Widerstände für größere Leistungen meist ein eigenes Gehäuse und werden separat aufgestellt.
RBR = Widerstand ?
UZ = Zwischenkreisspannung V
PBR = Bremsleistung W
Referenzen
Kunde / Produkt |
System, Sonstiges |
ABB |
- Stahlgitterwiderstände BEG
- gekapselter Widerstand VPR
- Drahtgewickelter zementierter Widerstand
|
Emotron |
- Stahlgitterwiderstände BEG
- drahtgewickelter zementierter Widerstand DEZ
|
Lenze |
- Stahlgitterwiderstände BEG
- gekapselter Widerstand VPR
|
Maschinenfabrik Leimbach |
- Stahlgitterwiderstände BEG
- drahtgewickelter zementierter Widerstand DEZ
|
Moeller |
- Stahlgitterwiderstände BEG
- drahtgewickelter zementierter Widerstand DEZ
|
Omron |
- Stahlgitterwiderstände BEG
- drahtgewickelte zementierter Widerstand DEZ
|
Rekers |
- Stahlgitterwiderstände BEG
- gekapselter Widerstand
|
Schneider Electric |
- Stahlgitterwiderstände BEG
- gekapselter Widerstand VPR
- drahtgewickelter Widerstand VPR
|
Siemens AG |
- Stahlgitterwiderstände BEG
- gekapselter Widerstand VPR
|
Text © GINO AG |
|