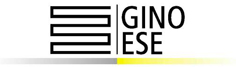 Motor starters
Application
Together with separate resistors, the motor starters start three-phase motors with slip-ring rotors of up to 2000 kW and rotor voltages of up to 2000 V.
The type and design of the motor starters can be freely selected from the resistor portfolio of this list and can thus be optimally adjusted to the individual application.
Structure
1PK4 motor starters are switching devices with contactors and timer modules, mounted in a control cabinet with feet for elevated installation. The control function is taken on by a Siemens LOGO! control or, alternatively, a time relay. In the case of the LOGO! control, the starting times can be adjusted by reprogramming with a "Yellow Card" and in the case of design with a time relay, it can be adjusted manually on the relay.
Stator circuit breakers and motor protection devices are not included.
With resistors to be ordered separately, the customer shall connect the power contactor connections to bridge the resistor steps. They shall be connected directly to the contactor contacts.
The cabinet door is equipped with signal lamps that indicate the switching steps and a key-operated ON/OFF switch.
Standard units are provided with Siemens air-break contactors, other designs are possible upon request.
The units can also be supplied as control resistors for the control of series resistors to achieve permanent speed reduction. The design will then be adjusted to the respective application.
Standard paint: synthetic resin varnish RAL 7032
Codes and standards
3PK4 motor starters comply with the specifications for low-voltage equipment DIN VDE 0660, DIN 46 062 and IEC 292-3.
They conform to the EU Low Voltage Directive of 19 February 1973.
Protection class
Pursuant to DIN 40 050: IP54
Resistance to climatic changes
The starters comply with the specifications of DIN 50 010 T1 and are suited for indoor, roofed outdoor and outdoor installation without weathering protection at varying conditions of condensation, industrial and see climates.
Ambient temperature range
-25 to +50°C
Design insulation voltage
3PK 4 size | Main circuit | max. admissible rotor standstill voltage |
10 – 12 | 690 V AC | 1320 V AC |
13 – 14 | 750 V AC | 1500 V AC |
15 – 16 | 1000 V AC | 2000 V AC |
Control voltage
Contactors and control units are designed for 230 V 50/60 Hz. A control power transformer can be supplied as an accessory (Table 5.3). This way, inlet voltages of 550-525-500-480-460-440-415-400-380-240 and 110 V can be adjusted. Other voltages can be realized if the customer inserts a series transformer.
Control
The motor starter is controlled via an installed ON/OFF key switch (-S10 in the circuit diagram on p. 4.5) wired to terminals so that the control can alternatively be taken over by superordinate switchgear.
Position indicator
For each step, a signaling lamp will show the switching position of the motor starter. The last signal lamp shows that the start is completed.
Auxiliary switch
An auxiliary switch on the output step / short circuit contactor signals the completion of the start to external circuits. The insulation voltage of the floating contact is 690 V AC.
Max. load for auxiliary switch:
Operating voltage V |
Nominal operating current AC11 ie A |
10 – 12 | 690 V AC |
13 – 14 | 750 V AC |
10 – 12 | 690 V AC |
Further auxiliary switches upon request.
Electronic blocking protection
Motor starters 3PK4 14 through 3PK4 16 can be equipped with electronic blocking protection. The blocking protection monitors the starting of the motor and interrupts the starting process if the motor is blocked and does not start.
Connection
To insert the connecting cables, the casing of the motor starter is provided with one or two flanged plates at the bottom where the requisite bores for line and cable inlet have to be made. Protective conductor terminal connection: 1 x M8 (2 x M8 starting from size 14)
Circuit diagrams
The basic design of the circuits is shown on the circuit diagrams on page 4.5. The resistors must be ordered separately. Only the circuit diagram supplied with the respective unit shall be applicable.
Text © GINO AG |
|